Blow-Fill-Seal Packaging
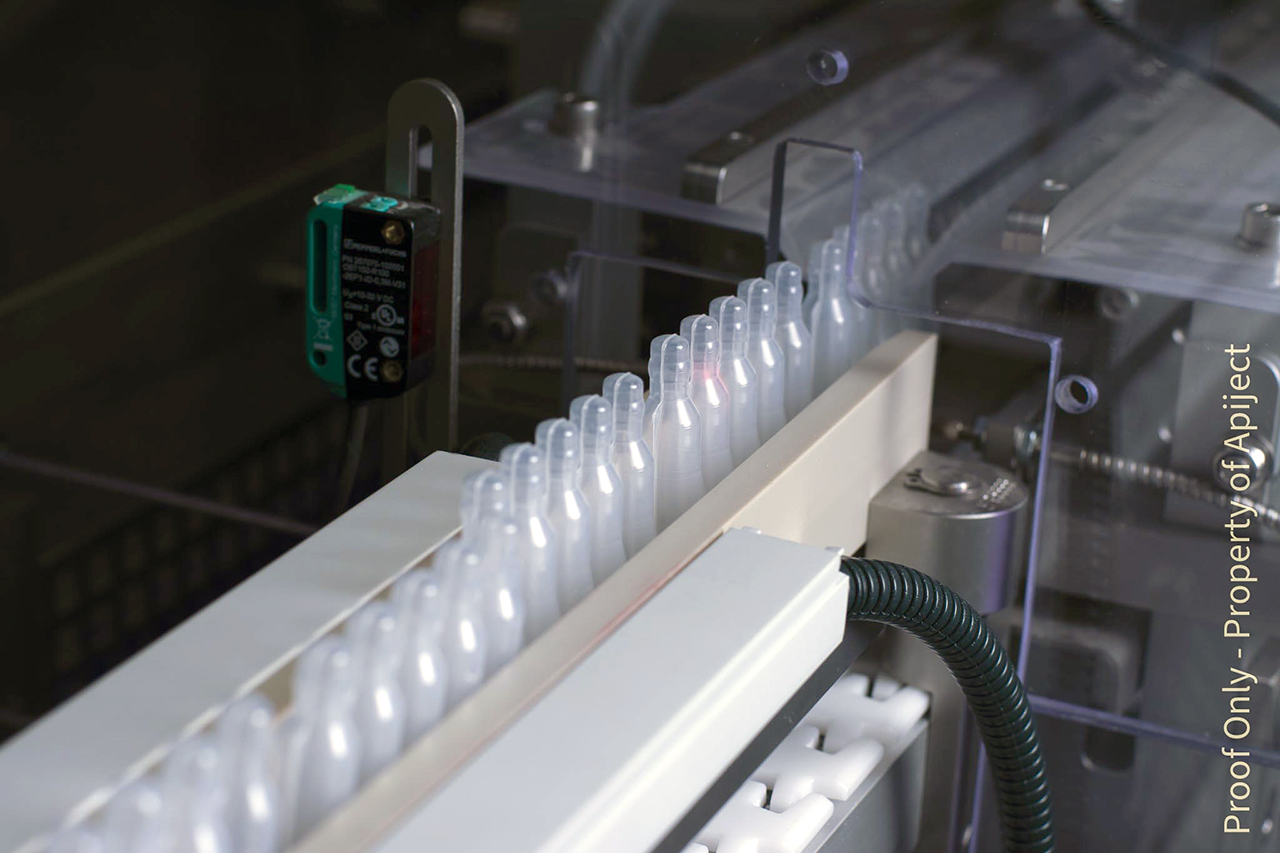
Blow-Fill-Seal (BFS) packaging has emerged as a seamless and efficient solution for liquid packaging in various industries. With its innovative container design, ApiJect is enhancing drug delivery through BFS technology.
The manufacturing process, coupled with protective foil overwrapping, ensures the integrity and safety of the products. Moreover, the compact design and space efficiency of BFS manufacturing offers a significant advantage in optimizing production facilities.
In comparison to traditional glass filling lines, BFS systems provide operational advantages that can revolutionize the packaging industry.
As we dive into the critical role of BFS molds in the process, we will uncover the key elements that make this packaging method both intriguing and indispensable for modern-day manufacturing.
Key Takeaways
- The BFS process combines container forming, liquid filling, and hermetic sealing in one continuous cycle, ensuring sterility and product integrity.
- ApiJect's innovative BFS container design allows for easy administration of drug products and enables attachment of non-BFS components, increasing versatility.
- The manufacturing process includes engraving or labeling important information on the container, removing excess plastic, and inspecting for quality before protective foil overwrapping which protects from moisture and gas permeation.
- BFS machines are compact, requiring minimal space and little human intervention, making them more efficient and cost-effective compared to glass filling lines.
Blow-Fill-Seal Liquid Packaging Process: A Seamless and Efficient Cycle
The BFS liquid packaging process is a highly efficient and seamless cycle that takes place within a single machine or production line.
This innovative Blow-Fill-Seal technology combines the forming of the container, filling it with the liquid product, and hermetically sealing the container's opening all in one continuous process.
The aseptic BFS process ensures the highest level of sterility and product integrity.
The pharmaceutical-grade plastic resin beads are heated and extruded to form the container, which is then filled with the sterile liquid through a filling mandrel.
The containers are sealed using a set of molds, and the finished BFS containers are inspected for quality before being prepared for packaging.
This efficient and aseptic filling method has revolutionized pharmaceutical technology, providing a reliable and cost-effective solution for packaging liquid products.
Enhancing Drug Delivery with ApiJect's Innovative BFS Container Design
ApiJect's innovative BFS container design revolutionizes drug delivery by allowing for easy administration of the drug product from a single prefilled device. This design approach enables users to attach non-BFS components to the BFS container, expanding its versatility in various administration routes.
The benefits of this innovative design are evident in ApiJect's first drug delivery system for intramuscular injections, which combines a pen needle-style hub with a BFS container. By bringing together BFS and attachable plastic components, ApiJect is unlocking the potential for BFS to serve as the central core element for single-dose prefilled drug delivery systems.
This approach enhances drug delivery by providing the following advantages:
- Simplified manufacturing scale and supply chain
- Cost efficiency compared to traditional prefilled syringes
- Wide range of administration routes, including parenteral and nasal
- Compatibility with aseptic BFS technology for sterile drug products
This innovative design is revolutionizing pharmaceutical packaging and paving the way for more efficient and convenient drug administration.
Manufacturing Process and Protective Foil Overwrapping in BFS Container Production
In the manufacturing process of BFS container production, after the filling and sealing of the containers, an engraver may be used to laser-etch important information onto the label tab.
This engraving process allows for the inclusion of important details such as the date, drug product, and batch number. Alternatively, a label machine can be used at a later stage if engraving is not done initially. Once the containers are filled, sealed, and engraved, they are moved to a punching machine that removes excess plastic, resulting in a clean strip of BFS containers.
Depending on the number of units, the strip may then be separated into cards using a separation machine. After inspection and quality control, the BFS containers or cards are typically wrapped in a hermetically sealed foil pouch.
Compact Design and Space Efficiency in Blow-Fill-Seal Manufacturing
After discussing the manufacturing process and protective foil overwrapping in BFS container production, we now turn our attention to the compact design and space efficiency in Blow-Fill-Seal manufacturing.
The Blow-Fill-Seal (BFS) packaging process offers a compact design that maximizes space efficiency in manufacturing facilities. Here are some key points regarding the compact design and space efficiency of BFS manufacturing:
- BFS machines are highly reliable and require little human intervention, resulting in good manufacturing space usage.
- The BFS filling suite only requires around 500 sq ft of space, compared to three times that size for a traditional filling line.
- The secondary packaging line for BFS can take as little as 1,200 additional sq ft.
- The entire BFS process can take place in a single facility since plastic ampoules are manufactured, filled, and sealed in one location.
This compact design and space efficiency not only optimize manufacturing space but also ensure the protection of the product from light and other external factors.
Operational Advantages in Efficiency: Blow-Fill-Seal vs. Glass Filling Lines
Blow-Fill-Seal (BFS) packaging offers operational advantages in efficiency when compared to glass filling lines. The smaller footprint of the BFS filler and the overall lower footprint of the entire line contribute to its efficiency. This is particularly evident when comparing the net relative output of a BFS line to a glass filling line or prefilled syringe line of similar size. Additionally, the filling efficiency of BFS is on par with or better than an equivalent glass line, with nominal ranges of 90-95%. However, design factors such as the distance of filling vessels from the fillers, compounding batch size ranges, tank volumes, piping arrangements, and IPC requirements can impact these efficiency measurements.
Critical Role of BFS Molds in the Blow-Fill-Seal Process
The BFS molds play a critical role in ensuring the success of the Blow-Fill-Seal process by shaping and sizing the containers for efficient dose delivery. Here are some key points to understand the importance of BFS molds in the Blow-Fill-Seal process:
- The BFS mold is installed into the BFS machine to form the container shape and size.
- Different machine models require different numbers of BFS molds, ranging from a single mold to a set of up to 20 duplicate molds.
- Production BFS molds are typically made of an aluminum bronze alloy and undergo rigorous testing before being used.
- The shape of the BFS mold is crucial as it affects the performance of the container and the ability of the drug product to be successfully filled and survive stability testing.
Top Questions Answered by Experts
What is a Blow-Fill-Seal product?
A Blow-Fill-Seal product is a type of packaging created by molding, filling, and sealing all in one continuous process. It is commonly used for pharmaceuticals, offering advantages such as sterility and tamper resistance.
What is the BFS container?
The BFS bottle is a type of plastic container used for packaging pharmaceutical products. It is known for its durability and safety, making it a popular choice in the industry.
What are the different types of BFS machines?
The different types of Blow-Fill-Seal machines are shuttle and rotary. A shuttle type machine uses a linear motion carriage to move a single mold set horizontally between the plastic extruder and the fill system. A rotary machine utilizes a single mold set or multiple mold sets that move vertically below the integrated extruder and fill system hardware.